Preventing chemical accidents in the workplace is crucial for maintaining a safe and productive environment. Chemical accidents can lead to serious injuries, health issues, and even fatalities. In this article, we’ll explore effective strategies for preventing chemical accidents in the workplace and ensuring the safety of all employees.
1. Understand Chemical Hazards
The first step in preventing chemical accidents is understanding the hazards associated with the chemicals you use. Each chemical has unique properties and potential risks. By knowing these hazards, you can take appropriate precautions to avoid accidents.
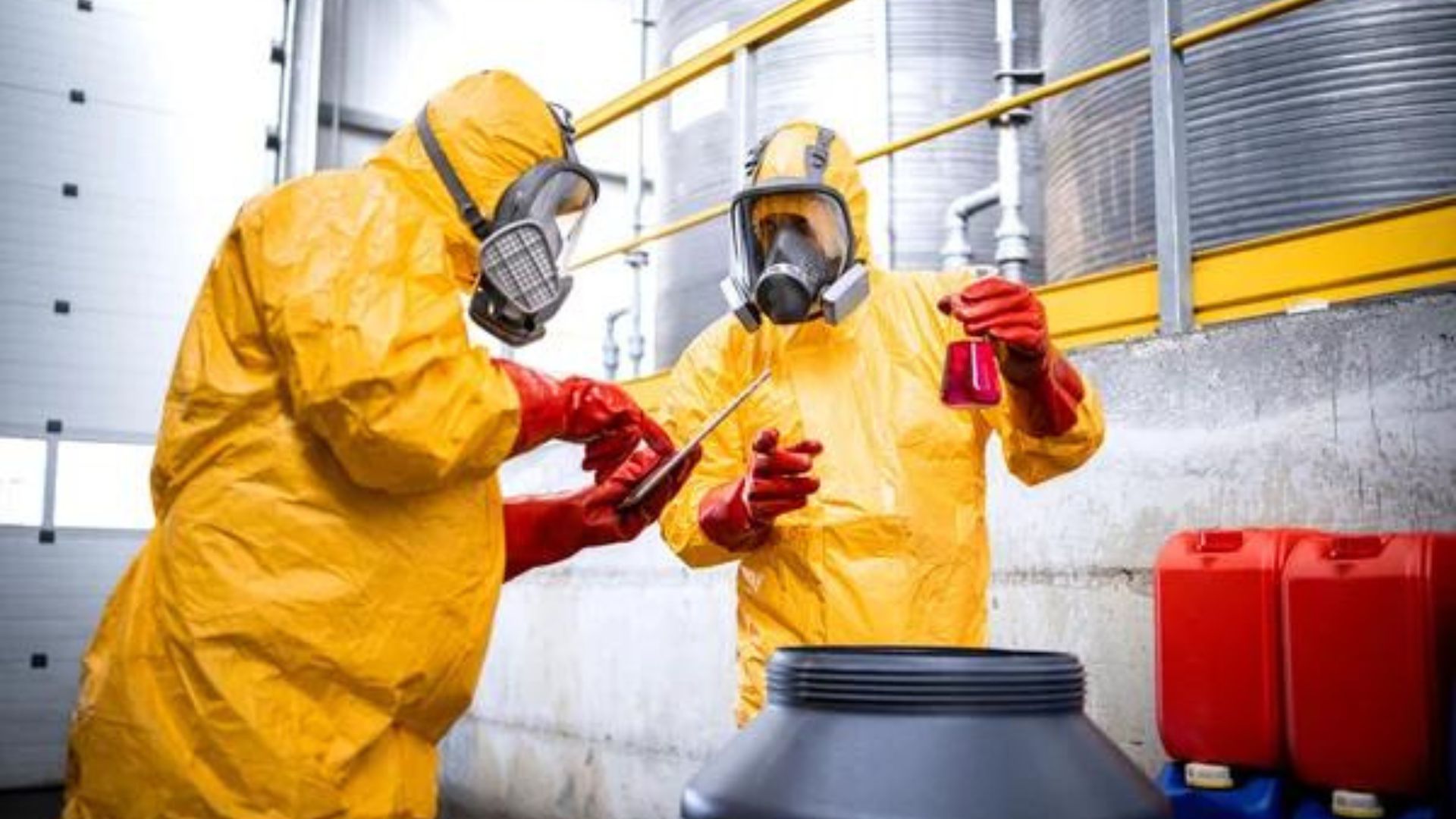
Preventing Chemical Accidents in the Workplace
2. Implement Proper Training
Training is essential for preventing chemical accidents. Ensure that all employees are trained on how to handle, store, and dispose of chemicals safely. Regular training sessions can keep everyone updated on the latest safety procedures and reinforce the importance of safety practices.
3. Use Safety Data Sheets
Safety Data Sheets (SDS) provide detailed information about each chemical, including its hazards and safe handling procedures. Make sure SDS are readily available for all chemicals used in the workplace. Employees should know how to read and use these sheets to prevent accidents.
4. Ensure Proper Storage
Proper storage of chemicals is key to preventing accidents. Store chemicals in appropriate containers and label them clearly. Keep incompatible chemicals separate to avoid dangerous reactions. Additionally, use secure storage areas to prevent unauthorized access.
5. Maintain a Clean Workspace
A clean and organized workspace reduces the risk of chemical accidents. Regularly clean work areas and promptly address any spills or leaks. Ensure that chemicals are not left out in the open where they can be accidentally knocked over or misused.
6. Provide Personal Protective Equipment
Personal Protective Equipment (PPE) is crucial for protecting employees from chemical hazards. Ensure that appropriate PPE, such as gloves, goggles, and respirators, is available and used correctly. Regularly inspect and replace damaged PPE to maintain its effectiveness.
7. Implement Emergency Procedures
Having clear emergency procedures in place can save lives during a chemical accident. Ensure that employees know what to do in case of a spill, fire, or exposure. Conduct regular emergency drills to keep everyone prepared for potential accidents.
8. Use Proper Ventilation
Good ventilation helps to prevent the buildup of hazardous fumes and vapours. Ensure that work areas are well-ventilated and that ventilation systems are regularly maintained. This can significantly reduce the risk of inhalation hazards and chemical exposure.
9. Monitor Chemical Use
Monitoring the use of chemicals can help identify potential risks and prevent accidents. Keep records of chemical inventories and usage. Regularly review these records to identify any patterns or issues that need to be addressed.
10. Conduct Regular Inspections
Regular inspections are essential for identifying potential hazards before they lead to accidents. Inspect storage areas, equipment, and workspaces for signs of wear, damage, or improper practices. Address any issues promptly to maintain a safe environment.
11. Encourage Reporting of Hazards
Encouraging employees to report potential hazards can prevent accidents. Create a culture where employees feel comfortable reporting safety concerns without fear of retaliation. Promptly investigate and address any reported hazards.
12. Label Chemicals Clearly
Clear labelling of chemicals is crucial for preventing accidents. Ensure that all chemical containers are labelled with their contents and hazard information. Use standardized labelling systems to avoid confusion and ensure that everyone understands the labels.
13. Limit Chemical Exposure
Limiting exposure to hazardous chemicals reduces the risk of accidents and health issues. Implement procedures to minimize the amount of time employees spend handling dangerous chemicals. Use automated systems when possible to reduce direct contact.
14. Stay Informed About Regulations
Staying informed about regulations and best practices is essential for preventing chemical accidents. Keep up-to-date with local, state, and federal regulations regarding chemical safety. Implement any required changes to comply with these regulations.
15. Foster a Safety Culture
Fostering a safety culture in the workplace encourages everyone to prioritize safety. Promotes open communication about safety concerns and continuously reinforces the importance of following safety procedures. Recognize and reward safe practices to motivate employees to stay vigilant.
Conclusion
Preventing chemical accidents in the workplace requires a combination of proper training, safety measures, and a culture of vigilance. By understanding chemical hazards, implementing safety procedures, and fostering a proactive safety culture, you can significantly reduce the risk of accidents and ensure a safe working environment for all employees.
Meta Description:
Learn essential strategies for preventing chemical accidents in the workplace. From proper training and storage to using safety data sheets and personal protective equipment, discover effective methods to ensure a safe and accident-free environment.