Chemical manufacturing relies on various reagents to synthesize products and carry out reactions. These reagents are essential for ensuring that processes are efficient and outcomes are predictable. Here’s a look at some of the most commonly used reagents in the industry:
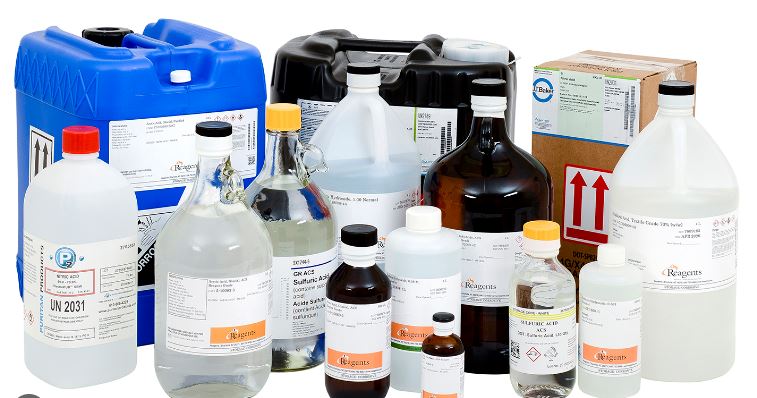
Common Reagents in Chemical Manufacturing
Acids and Bases
Acids and bases play a crucial role in many chemical reactions. Strong acids like sulfuric acid (H₂SO₄) and hydrochloric acid (HCl) are used for their reactivity in processes such as esterification and hydrolysis. Bases like sodium hydroxide (NaOH) and potassium hydroxide (KOH) are equally important, especially in neutralization reactions and saponification processes. Their ability to alter pH levels significantly influences the rate and direction of reactions in manufacturing settings.
Oxidizing and Reducing Agents
Oxidizing agents like potassium permanganate (KMnO₄) and hydrogen peroxide (H₂O₂) are essential for reactions that require the addition of oxygen or removal of electrons. Conversely, reducing agents such as sodium borohydride (NaBH₄) and lithium aluminum hydride (LiAlH₄) are used to donate electrons and hydrogen, facilitating reduction reactions. Both types of agents are critical in organic synthesis and industrial chemical transformations.
Solvents
Solvents are pivotal in chemical reactions for dissolving reagents and facilitating interactions between different chemical species. Common solvents include water, acetone, ethanol, and dichloromethane. Each solvent has specific properties that make it suitable for particular reactions, such as solubility, boiling point, and chemical reactivity. The choice of solvent can influence the efficiency and yield of the chemical process.
Catalysts
Catalysts accelerate chemical reactions without consuming themselves in the process. Common examples include transition metals like platinum, palladium, and nickel. These catalysts facilitate various reactions including hydrogenation, polymerization, and catalytic cracking in petroleum refining.Their ability to lower the activation energy of reactions makes them invaluable in both laboratory and industrial settings.
Complexing Agents
Complexing agents, also known as chelating agents, enhance the solubility and reactivity of metal ions by forming complex compounds with them. Ethylenediaminetetraacetic acid (EDTA) and citric acid are examples of such agents. They are particularly useful in water treatment, analytical chemistry, and as stabilizers in various industrial processes.
Reducing Agents
Reducing agents such as sodium dithionite and zinc dust are essential for reactions that require the addition of electrons to a chemical species. They are widely used in the textile and dye industries, as well as in the synthesis of various chemicals. Their ability to provide electrons makes them crucial for reduction processes in chemical manufacturing.
Specialty Reagents
Specialty reagents tailored for specific applications often include organometallic compounds and high-purity chemicals. These reagents find use in niche applications such as pharmaceutical synthesis, electronic materials production, and high-precision chemical reactions.
Conclusion
In summary, common reagents in chemical manufacturing are vital for the successful execution of chemical reactions. Their diverse roles—from adjusting pH levels and facilitating electron transfer to acting as solvents and catalysts—highlight their importance in producing a wide range of products. Understanding the function and application of these reagents ensures efficient and effective chemical manufacturing processes.